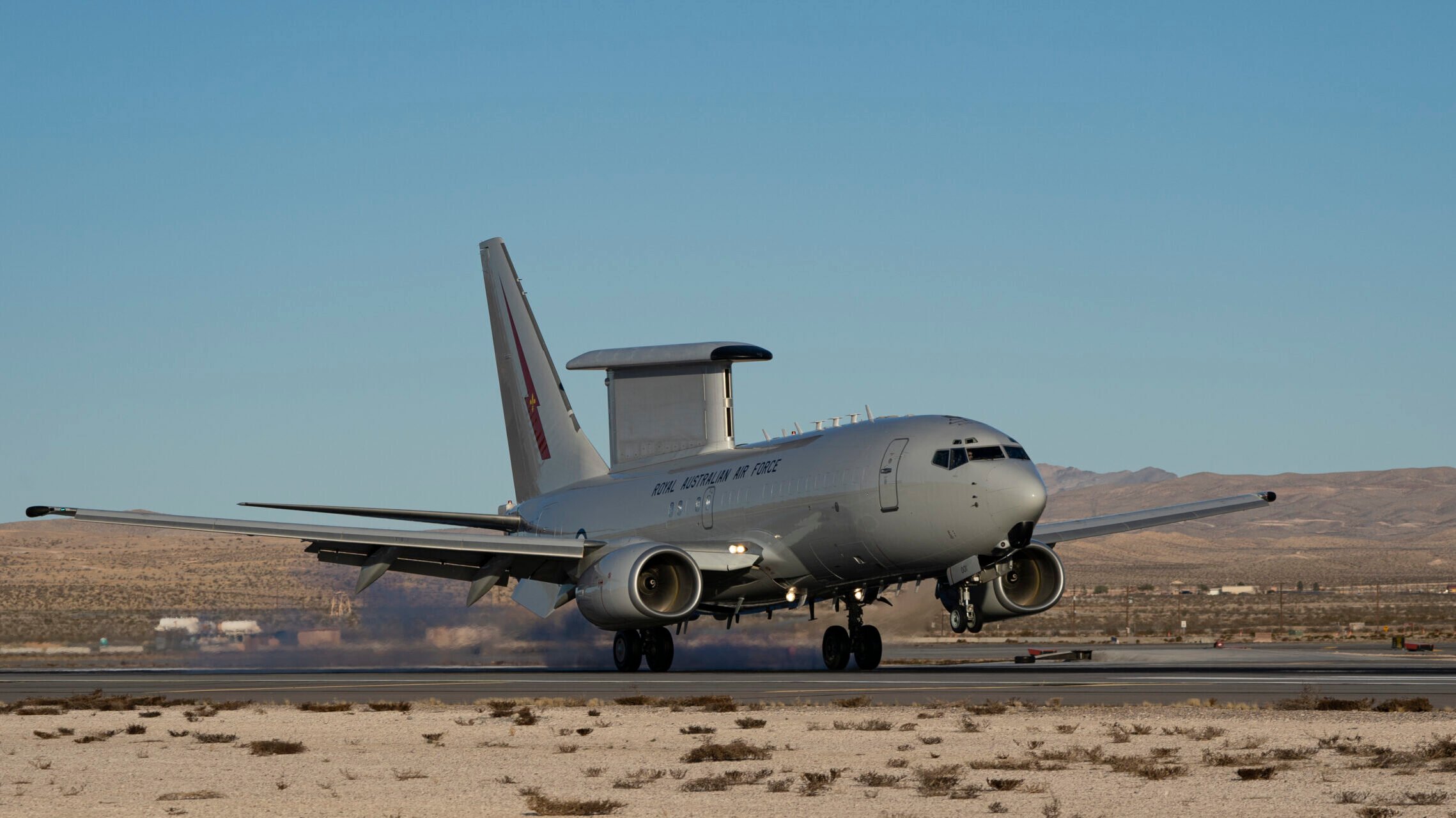
A Royal Australian Air Force E-7A Wedgetail airborne early warning and control aircraft lands at Nellis Air Force Base, Nevada, Jan. 30. 2020. (U.S. Air Force Photo William R. Lewis)
TUKWILA and RENTON, Wash. — Aerospace giant Boeing plans to ramp up production of the E-7 Wedgetail to an ambitious six planes per year to keep up with burgeoning global demand, according to the company official charged with getting the early warning birds in the air.
Previously, executives discussed plans for producing four of the radar planes a year with the possibility of reaching up to six. But in a December interview with Breaking Defense inside a trailer that houses a partial mockup of the Wedgetail’s interior at Boeing’s Tukwila Development Center, E-7 program manager Stu Voboril said it’s become obvious the company will shoot for the higher end as legacy airframes are phased out.
Pointing to orders from the US Air Force and now a recent win from NATO, Voboril said, “We’re working to get to a capacity of six per year. That’s where we think we need to be,” adding that the company aimed to reach that goal around the later part of this decade.
“As the [E-3] AWACS retirements are occurring globally, there’s a gap. So we’re trying to fit this within the gap of where the retirement of the AWACS fleet is right now,” he said.
The US Air Force, which now intends to buy 26 Wedgetails, expects its first two rapid prototypes to arrive by 2027 and that the remaining aircraft in the fleet will be delivered by 2032. The new aircraft is set to replace a fleet of 31 E-3 Sentry aircraft, a platform the service is rapidly divesting.
In November, Boeing’s E-7 prevailed in a competition to replenish NATO’s own E-3 early warning fleet, where the alliance has set a minimum order of six aircraft. NATO now wants its first E-7 by 2031 and has stated that its incumbent E-3 fleet should be retired around 2035.
Three E-7s are separately being built by Boeing in the UK for the Royal Air Force, which Voboril said is his team’s “number one priority.” Voboril also said there is “heavy dialogue” with Korea about expanding its current fleet.
In the US, there’s been a great deal of focus on accelerating the E-7’s procurement. Boeing and Air Force officials, however, have stressed the early rapid prototypes can’t be built faster, and only later aircraft production can be sped up if long-lead parts are purchased early.
Some Air Force officials have additionally pointed to the aircraft’s signature top hat radar — Northrop Grumman’s Multi-role Electronically Scanned Array (MESA) — as a possible limiting factor in production. But Voboril said the supplier is now preparing to build six MESAs a year that Boeing will need, a target that has also been confirmed by Northrop executives.
So far, Boeing has had some trouble recently fulfilling the UK order. The first of the UK’s E-7s were originally set to be delivered by the end of 2023, but now the first delivery isn’t due until this year because of what government officials attributed in part to “contractor performance” problems and supply chain woes. Additionally, more flight safety certification work was needed to comply with measures taken after the two separate crashes of 737 MAX jets — the successor design of the airframe used for the E-7 — in 2018 and 2019, officials said.
“We will take the time that’s required to get safety [and] quality and make sure their certification authority is happy with what we’re doing,” Voboril said of the UK’s E-7 program. He deferred questions on the program’s timeline for initial operational capability to the Royal Air Force, which a July 2023 procurement report from UK lawmakers warned might not be reached until 2025.
Boeing’s performance in this case, as well as other well-documented issues in its defense business, have made some analysts skeptical about the path ahead.
“There’s clearly a growing market for the E-7. The line’s survival was in doubt at one point, and it’s now heading towards record output. But Boeing’s track record on execution, even for mature platforms, is dismal, at best,” Richard Aboulafia, managing director at AeroDynamic Advisory who has often been critical of Boeing, observed in an email to Breaking Defense.
“But on the other hand the core of the system comes from Northrop Grumman,” Aboulafia added, referring to the MESA. “[S]o there’s hope.”
With the Air Force’s own E-3 fleet quickly aging out and other options like space-based moving target indication still years away, boosting the E-7’s production rate will be critical for meeting combatant command demands and sustaining a healthy pool of operators, Mitchell Institute Executive Director Doug Birkey told Breaking Defense.
“It’s going to be tight, even with the production boost. The real factors tie to suppliers, not Boeing,” Birkey said in an email, pointing to the aircraft’s radar and various specialized mission systems.
“It’s hard to move the needle on those types of nuanced skill sets — both from a workforce, tooling, and material perspective. Things like extended CRs [continuing resolutions] don’t help, for they cut into the advanced funding and predictability required to grow the ability to produce in higher numbers,” he added.
Building The E-7
The E-7 is a military derivative of Boeing’s narrowbody 737 Next Generation (NG) commercial jet, built by the aerospace company in the Seattle suburb of Renton, Wash. The 737NG, the predecessor of the 737 MAX, also forms the baseline of other military aircraft like the Navy’s P-8 Poseidon. (Boeing delivered the final commercial 737NG in 2020.)
The P-8, which is also produced for foreign customers, has some newcomers still: a national flag for each of the plane’s buyers hangs above the line, and Canada’s was added just a day before Breaking Defense’s visit.
Forthcoming E-7s like those ordered by the US Air Force will be produced on the same line as the P-8 in Renton. Here, Boeing receives fuselages from supplier Spirit AeroSystems by rail, which are then hauled into the factory and joined with wings on an assembly line. Other features like electrical wiring are also furnished on the line before aircraft like the P-8 and eventually the E-7 are shipped out for military conversion.
Speaking from inside the upper deck of a P-8 undergoing assembly at the aircraft’s production line in Renton in December, P-8 program manager for Boeing Commercial Airplanes Michael Meyer said his task is to deliver a “flying wire bundle” to Boeing’s defense division, pointing to countless exposed wires running throughout the cabin. His goal, he said, is minimizing tasks like drilling for his counterparts tasked with military conversion.
For the E-7 at least, that work will be especially complex: Along with various battle management, defensive and support systems, the aircraft’s huge MESA radar will also need to be carefully installed by opening up and strengthening the fuselage.
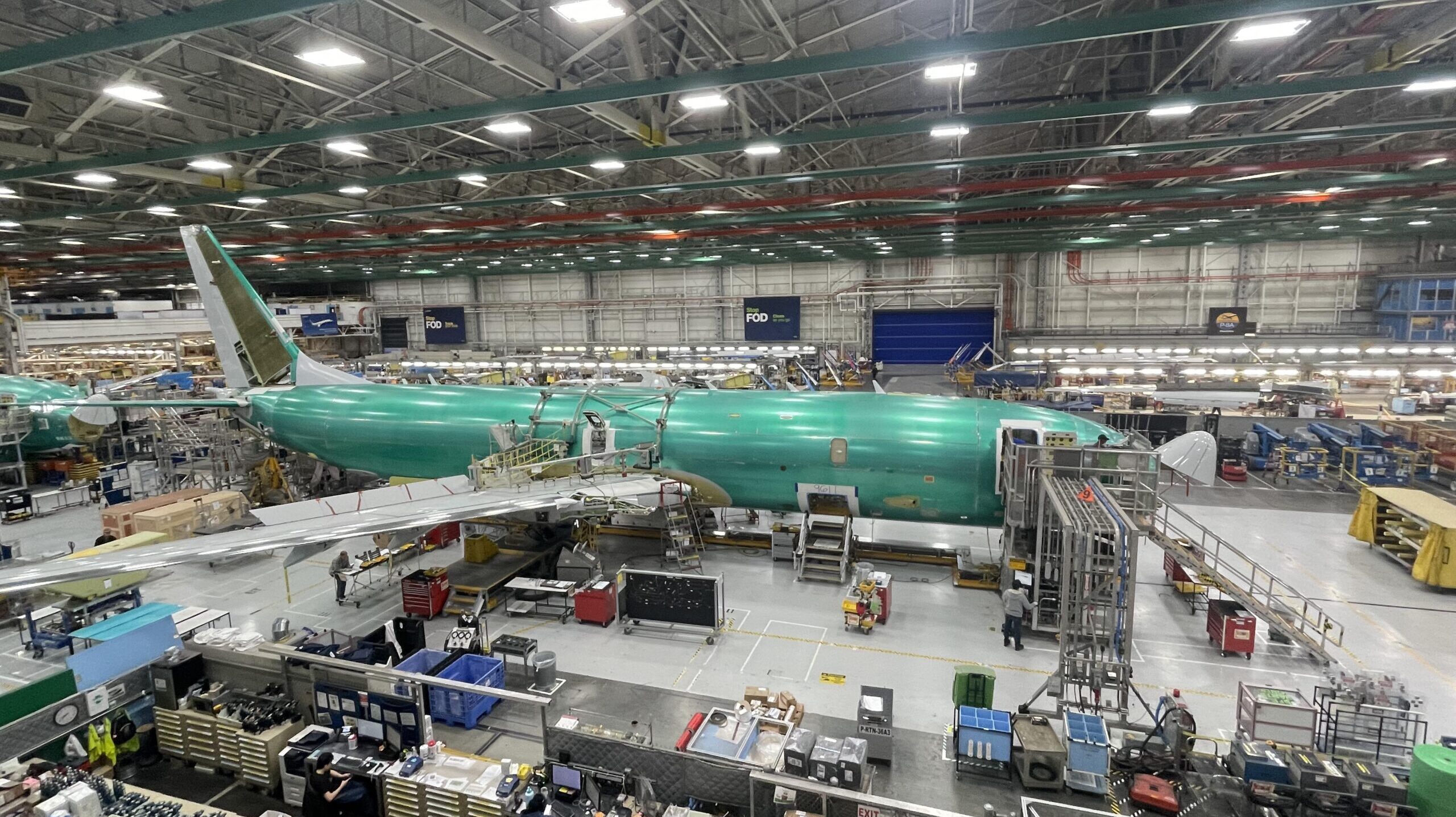
A P-8 maritime patrol aircraft undergoes assembly at Boeing’s Renton production line. Future E-7s, based on the 737NG, will be slotted into this line for assembly. (Michael Marrow/Breaking Defense)
Across Boeing, different programs are experimenting with new manufacturing techniques to maximize efficiency and speed up production, though results have been mixed at times. For example, the F-15EX program in St. Louis hit a stumbling block when incorporating full-size determinant assembly. The company emphasizes lessons learned will smooth the road ahead.
With a more relaxed production tempo compared to mainline 737 production, Meyer said his line is more tolerant of risk associated with incorporating new techniques and technologies, making him more willing to try things out.
“Because I’m at a slower rate, I have been trying to demo some things for [the] mainline like I do here,” he said, speaking over the roar of power tools as workers behind him joined together an aircraft’s wing and body.
Renton is also no exception to the supply chain snarls that have been the bane of the aerospace industry in recent years, though Meyer said some things are improving.
Late 2022 and early 2023 “was really a supply chain nightmare,” he said. “My sense, at least from my line, is we’re getting more stable. But it is not a step change, it is a glide slope.”
Meyer explained the struggle for parts is often centered around “specialty” items, like particular valves and control units, though it’s been difficult to find a “common theme” troubling the supply chain. He did however identify one widespread pattern: workforce disruptions.
When the pandemic hit, droves of engineers and other key workers retired, which Meyer said consolidated about five years worth of retirements into nine months. The churning workforce also introduced new employees without as much experience, who in turn required more training.
“We’re hearing the same thing throughout our industry partners,” Meyer said. “There’s a ringing through the industry.”
Boeing’s Wedgetail ‘Vision’
Flying in the Wedgetail, operators are seated at large terminals with interactive displays, which process sensor data to map out enemy, ally, and unknown objects to help manage a battlespace. Voboril said Boeing’s “vision” is for those operators to focus on different domains but have the ability to seamlessly switch between them on the same display if need be, whose tasks will be aided by automated tools and integrated communications across platforms.
According to Voboril, Boeing’s plan is for the E-7 to serve roles beyond battle management, encompassing a wide range of tasks, such as controlling other assets like drone wingmen known in the Air Force as collaborative combat aircraft (CCA). Battle managers could do that at their same terminals they use for their other tasks, Voboril explained.
The Air Force hasn’t formally decided if or how E-7s will operate CCA, Voboril clarified, reasoning that the company is planning to offer the capability in case the service goes that route. And as Boeing works with the Air Force on the architecture, the UK and Australia have expressed interest in the capability and are actively participating in technology review meetings as well, he said.
Voboril additionally said his team is trying to design the E-7 with the ability to evolve, pointing to features like open architectures and margin for upgrades. Future improvements will likely require greater electrical power and cooling — a problem spurring modernization efforts for top programs like the F-35 — and Voboril said the power generation stemming from the aircraft’s dual CFM56 engines will help provide room for growth.
When the Air Force issued Boeing an up to $1.2 billion contract to kick off E-7 production nearly a year ago, the award was made as an undefinitized contract action, meaning that early work could start as the Air Force and Boeing ironed out specifics like terms and prices. Voboril said both parties are aiming to finish the contracting process this year, finalizing the Air Force’s order.
Part of that process will also be tying up negotiations over data rights, which when obtained from contractors can facilitate greater service-led maintenance or competition for sustainment. Data rights can particularly be a sticking point in negotiations, most recently reportedly serving as a factor in Boeing’s elimination to build a replacement for the E-4B “Doomsday Plane.”
But according to Voboril, negotiations on the E-7 for data rights should be wrapped up soon.
“I think that has gone actually really well,” he said, adding that no “major concerns” remain. “I think we are almost at the finish line,” he said, noting that those discussions will not hold back finalizing the aircraft’s contract.
As both the Air Force and Boeing move forward on the program, Voboril emphasized that the company will be able to draw from its “playbook” of building the E-7, and that work right now is focused on “get[ting] the platform right” to ensure it meets the service’s requirements.
“It’s more of: Get the architecture and what this needs to do for growth and support all the missions and the growth of the missions. And then we go into production,” he said.
Laser weapons and future tanks: European Defense Fund to spend $1.3B on 54 projects
Development of more novel weapon systems includes the second phase launch of the Tactical Advanced Laser Optical Systems (TALOS) project (TALOS-TWO), designed to support a long term target of developing 100 kilowatt-class laser weapons by 2030.